Optimising industrial production by using data from machines and sensing devices
The KAP approach (Knowledge – Awareness – Prediction). KAP (Knowledge of past performance and Awareness of the present state, enabling the Prediction of future outcomes) aims at providing manufacturing standards in an holistic approach for achieving energy efficiency in industry. To this end, KAP focussed on defining production indicators that included sustainability criteria and energy efficiency.
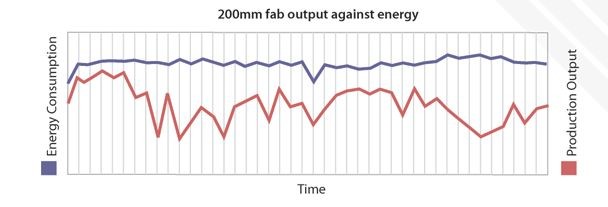
The challenge
Within industry, it has been well established that energy could no longer be considered a fixed operational expense, due to rising energy prices and taxes related to carbon footprint. From then on, sustainable manufacturing became a crucial issue for production managers in order to reduce the environmental impact with regard to production practices. In addition, the “green” aspect of a product turned out to be a key parameter in consumers’ act of responsible purchasing. Yet, existing support tools such as MES (Manufacturing Execution Systems), ERP (Enterprise Resource Planning) and SCADA (Supervisory Control And Data Acquisition) were not capable of providing an holistic optimisation of sustainable production processes but used to provide only targeted views. Such tools required production managers to aggregate and integrate spread information. KAP addressed this challenge by designing a global approach for managing and optimising production processes.
The innovation
The KAP was a European research project completed in December 2013. Co-financed by the EU FP 7 grant funding programme, the project was coordinated by SAP (Germany), well-known business software expert, and gathered key players from the electronics and software sectors (Microsoft, Atos…) and some major end-user industrials (Nissan, Volvo, Infineon, Intel), as well as research centres and universities.
KAP addressed the weaknesses of the existing management tools, i.e.:
the separation of real-time monitoring from business intelligence,the absence of predictive models,the absence of a feedback loop that would allow the system to learn from the quality of its predictions.
Diagram: courtesy http://www.kap-project.eu/
The approach developed within KAP brought important innovations concerning the key elements impacting the optimisation of production processes; i.e. the four M’s (Man, Machine, Material and Method).
To go beyond the existing tools and models, it was first assumed that setting energy standards could ensure that energy should be managed with the same level of attention as other materials within production processes. Therefore, a set of new production performance indicators (PPI) was defined. In this context, the key innovation was based on “computational learning” techniques. By applying complex event processing (CEP) models to past and current PPI levels, future outcomes could then be predicted. This method aimed at adjusting accuracy and creating a self-improving operational control system. In addition, an efficient man-machine interface was designed to communicate PPIs toward production managers in order to reduce cognitive workload as well as to highlight areas requiring intervention.
Why did it work?
The main motivation of KAP was to use existing resources as efficiently as possible rather than making additional investments in new resources. The distinctive feature of the KAP research project was to provide a standards-based approach built on a network of on-line sensing devices and smart IT regardless of the age or sophistication of industrial facilities.
Further deployment
The framework developed within KAP could be applicable to different production processes. The approach was demonstrated at prototype level in the semi-conductor industry and in the automotive industry. The level of maturity is therefore estimated to be 7 on the TRL scale.